Blog
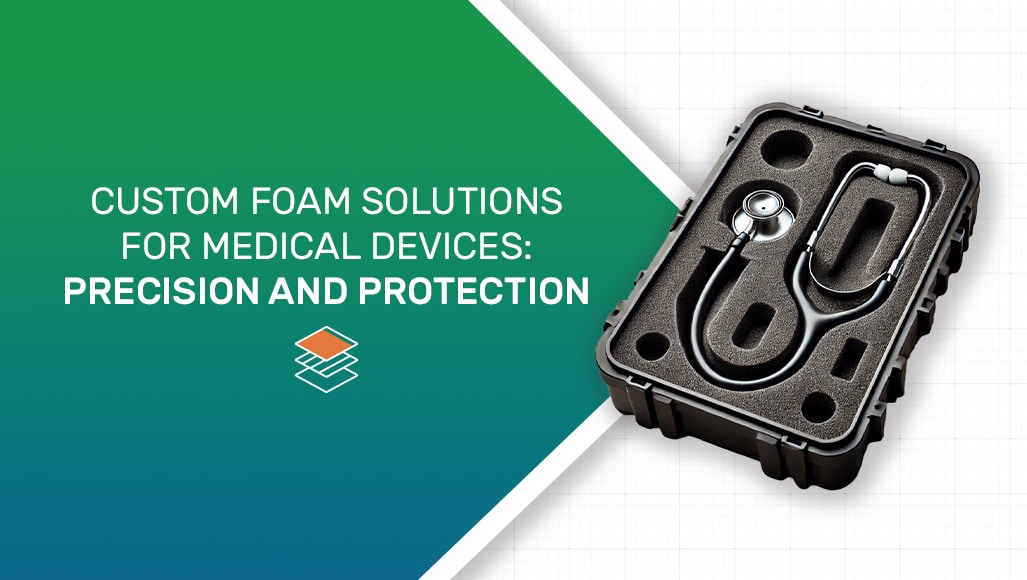
Custom Foam Solutions for Medical Devices: Precision and Protection
In the costly and highly regulated medical device industry, ensuring the safety, functionality, and longevity of products is critical. Packaging plays a vital role in this process, especially when dealing with delicate or precision instruments. Custom foam solutions have become a go-to option for medical device packaging because they provide a high level of protection while being tailored to the specific needs of the product.
We specialize in creating custom foam solutions that meet the demanding requirements of the healthcare sector. Our precision-engineered foam inserts, padding, and packaging are designed so that medical devices arrive at their destination in the same condition they left in.
Why Custom Foam Packaging is Ideal for Medical Devices
Medical devices come in all shapes and sizes, from small surgical instruments to large diagnostic machines. Off-the-shelf packaging options rarely provide the level of protection required for these specialized tools.
That’s where medical device packaging companies like American Foam Products step in. We offer custom foam solutions that are specifically tailored to:
- Protect sensitive components: Medical devices often contain fragile parts, from glass screens to tiny sensors. Custom foam ensures that each component is securely held in place, reducing the risk of damage during transport.
- Accommodate irregular shapes: Medical devices frequently have unique shapes that don’t fit standard packaging. Custom foam inserts can be precision-cut to cradle these items, providing full support and protection.
Types of Foam Used in Medical Device Packaging
We use advanced materials that offer excellent durability, chemical resistance, and cushioning properties. The materials described below are perfect for medical device packaging because of their unique properties:
- Closed-cell structure for excellent cushioning and shock absorption
- Chemical resistance and low moisture absorption
- Ideal for protecting sensitive medical equipment
- Open-cell structure for flexibility and comfort
- Available in various densities for different applications
- Suitable for cushioning and contouring around complex shapes
Cross-linked Polyethylene (XLPE) Foam:
- Enhanced durability and temperature resistance
- Excellent for repeated use and sterilization processes
- Provides superior protection for high-value medical devices
- Specially formulated to dissipate static electricity
- Crucial for protecting sensitive electronic medical equipment
- Helps prevent damage from electrostatic discharge
Why Foam Packaging Over Alternative Options?
Foam sets itself apart for its valuable properties that other packaging materials lack:
- Impact absorption: Medical devices are often transported long distances, exposing them to potential drops and impacts. Our foam is designed to absorb shock, ensuring the devices inside remain safe.
- Vibration dampening: Many medical devices are sensitive to vibrations. Our foam packaging minimizes vibration, protecting the internal components from malfunction.
- Lightweight yet sturdy: Medical devices can be heavy, but adding unnecessary weight with packaging can increase shipping costs. Custom foam is lightweight but durable, offering protection without adding bulk.
Specific Applications of Foam in Medical Device Packaging
You might be wondering what types of orders we see come in for medical device packaging. Here are some common use cases:
Instrument Trays and Kits: Custom foam inserts designed to securely hold surgical instruments, ensuring organization and protection during transportation.
Diagnostic Equipment Packaging: Precision-cut foam solutions that cradle sensitive diagnostic devices, such as ultrasound probes or portable X-ray machines, protecting them from shock and vibration during transit.
Implant Packaging: Biocompatible foam packaging for medical implants that maintain their integrity.
Laboratory Equipment Protection: Custom foam inserts for delicate laboratory instruments, such as microscopes or centrifuges, ensuring accurate calibration and functionality upon arrival.
Medical Device Shipping Cases: Rugged, foam-lined cases designed for the safe transport of medical devices in various environments, from hospitals to field clinics.
Custom Foam Packaging Solutions for Medical Device Companies
As a top medical device packaging company, we offer a range of customizable solutions for manufacturers. Our process goes like this:
- Consultation and design: We work closely with you to understand your product’s unique requirements, including dimensions and fragility. Our engineers then create a custom foam design that provides maximum protection.
- Material selection: Different medical devices require different levels of protection. We offer a variety of foam materials, including polyethylene, polyurethane, and cross-linked foams, to ensure that the right material is used for each product.
- Prototyping and testing: Once the design is finalized, we create a prototype for testing. This allows you to evaluate the packaging’s performance under real-world conditions before full production.
- Production and delivery: After the prototype is approved, we move to full-scale production. Our efficient processes ensure that your custom foam packaging is delivered on time and within budget.
Conclusion
When it comes to medical device packaging, precision and protection are essential. We understand that custom solutions are important, not only for compliance, but also for the safe delivery of your medical devices. Whether you’re packaging a simple instrument or a complex diagnostic tool, our custom foam solutions provide the reliability you need.
By partnering with us, medical device manufacturers can relax knowing their products will arrive unscathed, ready to save lives and improve patient outcomes. For medical device manufacturers, procurement specialists, and designers seeking the highest quality in custom foam solutions, we are your trusted partner.
Contact us today to learn more about how we can create custom foam solutions for your medical devices.