Blog
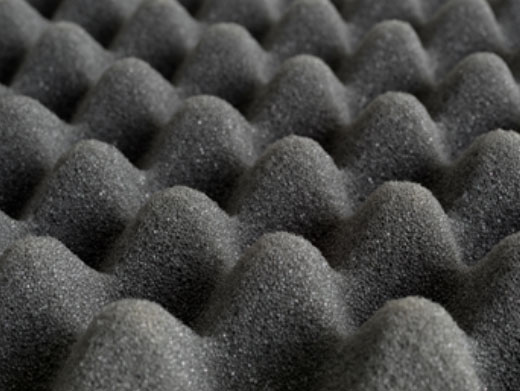
Dramatic Rise of Material Costs for Foam Fabricators and Foam Converters
Over the past eight months, foam fabricators and converters have been pummeled by a series of material cost increases from foam manufacturers due to a range of factors — most notably, a shortage of feedstock materials used in the foam manufacturing process.
In response to the COVID-19 pandemic’s worldwide impact in early 2020 and the uncertainty of demand during the pandemic, producers of critical foam feedstocks such as propylene oxide (PO) and toluene diisocyanate (TDI) reduced their output, and polyethylene and polyurethane foam manufacturers generally reduced their output as well.
However, with many people then hunkered down in their own homes due to lockdown measures, the demand for many foam-related products — particularly those for furniture and bedding-related items — rose sharply.
The feedstock producers eventually ramped back up and foam manufacturers sought to increase their output throughout the second half of 2020. However, the demand backlog, volatile freight costs, supply chain disruptions, COVID-19 effects on factory labor forces, and bad weather in the Gulf of Mexico region in the fall of 2020 created shortages and higher costs — and foam manufacturers began passing on their higher costs to their customers, including foam fabricators.
February Storms Affect Foam Production Feedstock
Propylene oxide is primarily produced in five manufacturing plants in the Gulf Coast region, and toluene diisocyanate is produced at two other manufacturing plants along the Gulf Coast. Resins used to manufacture polyethylenes also are produced in Gulf Coast manufacturing plants.
In February 2021, a crippling winter storm rolled through Texas and the Gulf region, causing over 100 deaths and significant material damage to manufacturing and distribution. Foam feedstock production was disrupted by the unprecedented record cold temperatures, which caused power outages at some facilities for several days, the loss of on-site nitrogen and hydrogen supplies, and freezing of service lines.
As a result, these production facilities had to restock and restore their supplies and make necessary repairs to recertify their processes for manufacturing both PO and TDI. In some cases, full repairs would take months to complete. In the interim, foam feedstock production rates have been well below normal.
Without sufficient feedstock, existing foam supplies cannot meet demand. This is particularly noticeable in the furniture and bedding sectors. Even automotive manufacturers have had foam shortages for their interiors.
Rising Costs for Foam Fabricators and Converters
Since Fall 2020, foam fabricators have incurred multiple cost increases from their raw foam suppliers — in some instances, only four weeks after the previous cost increase was implemented.
Since October 2020, American Foam Products has seen polyethylene costs increase by more than 20%, polyurethane costs increase for some materials by more than 40%, and expanded polystyrene costs increase by more than 20%. And, it is still possible that more cost increases will be passed on by the foam manufacturers.
As intermediaries, foam fabricators and converters provide value-added services on the foam that they source. Under normal circumstances, American Foam Products uses commercially reasonable efforts to minimize the impact of foam cost increases on its customers, especially if such increases occur on short notice or after customers have committed to certain costs for a given period. Nevertheless, foam fabricators such as American Foam Products are not able to control or absorb material cost increases from their suppliers of this magnitude without being forced to pass along such increases to their customers.
Of course, these circumstances are unusual. As foam feedstock supply issues are ironed out and costs come down, foam manufacturers may reduce some part of the cost increases that have been implemented — given the magnitude of these cost increases.
American Foam Products is Well Positioned to Handle the Foam Shortage
Since 1978, we’ve been manufacturing custom foam products to serve customers throughout North America. We’ve dealt with disruptions and supply-side delays before, and will do so again. With our experience and long-term history in the industry, we’re equipped to get what is needed to serve our customers.
With a diversified portfolio of product offerings, we can quickly adjust to the vagaries of the current landscape to propose solutions for your packaging, insert, or protection needs. We can offer Ester and Ether Polyurethane products but also address needs with Polyethylene or Polystyrene based solutions. From corrugated plastics to anti-static foam to pressure-sensitive adhesive, we’ve been able to design, develop, draft, and deliver needed products to keep your business on track.
Our team of experienced designers, engineers, and creators will ask the right questions and can meet any specifications for the job. We’ll leverage our experience to find the best solution for you. Custom fabrication is guided by creative solutions and problem solving, and both will be vital to help navigate the current climate of price increases amid this foam shortage.
Contact us today to put our expertise to work toward your packaging and protection needs.